
- Future-proof. Standardised and scalable solutions for every automation requirement
- Cost-effective. The right automation solutions in terms of ROI
- Smart. From flexible plug & play solutions to highly customised system solutions
- Competent. Rely on many years of experience and the largest portfolio of state-of-the-art transport systems (mobile and stationary)
- Predictable. Short response times in the design and quotation preparation stages, as well as in the implementation of projects
- Reliable. Tailored service packages, software-assisted maintenance and service processes and competent service teams in your area
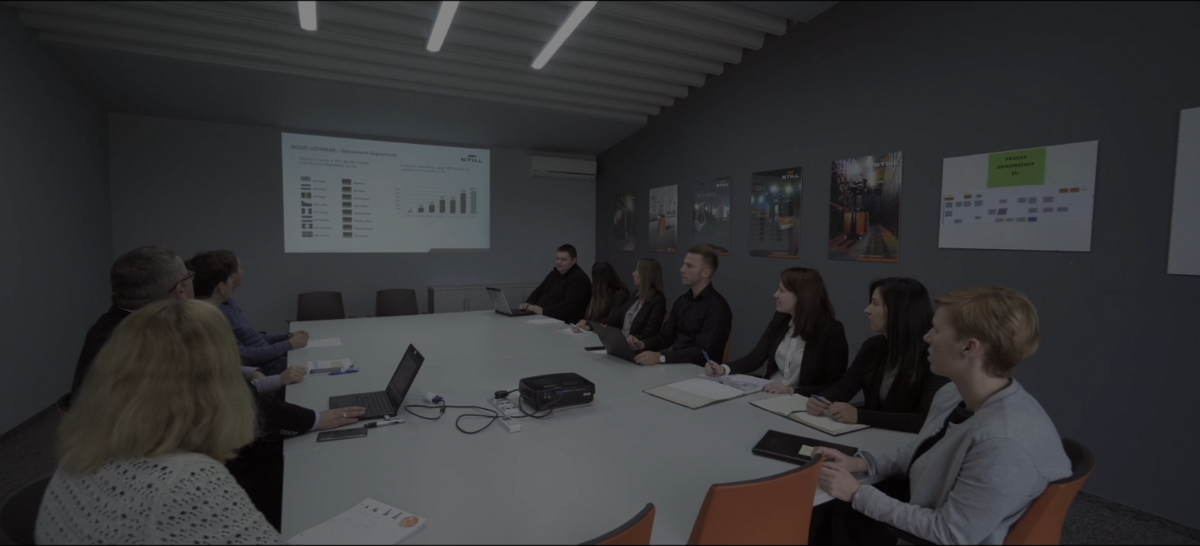
Request to: Automation in logistics
Please fill out the form below. We will get back to you as soon as possible.
STILL offers a wide range of different solutions and truck-based extension levels to help you automate your processes. They can be adapted to the complexity of your requirements, meaning that they are guaranteed to pay off every time.
Production supply and disposal / empty pallet transport
Lean production begins with the supply of raw materials for processing. Smooth supply ensures that production does not come to a standstill. These processes are usually also a good starting point for automation.
Our solution:
- Our autonomous mobile robots (AMR) are the smart solution for optimised horizontal material flow. Also for moving pallets when working with a transfer station.
- The automated all-rounder STILL EXV iGo high lift pallet truck ensures highly efficient logistics processes – as a stand-alone solution or in mixed operation with manual trucks. The truck picks up pallets directly from the floor without any additional hardware.
Customer reference:
Automated solution in use at the Hase Safety Group
Inbound & outbound
Take your intralogistics to the next level: Store incoming or outgoing pallets within a warehouse, move goods to production or to a material handling system – horizontally and vertically.
Our solution:
The automated all-rounder STILL EXV iGo high lift pallet truck ensures highly efficient logistics processes – as a stand-alone solution or in mixed operation with manual trucks. The truck picks up pallets directly from the floor without any additional hardware.
Customer reference:
Fully automated EXV high lift pallet trucks in action at
Danfoss Power Electronics A/S
Storage and retrieval (high bay)
High bay racking with very narrow aisles is one of the most effective ways of organising a warehouse in terms of volume utilisation. Typically, they involve repetitive handling tasks with standardised transfer stations and homogeneous load carriers.
Our solution:
The automated STILL MX-X iGo very narrow aisle truck is the ideal partner for warehouses with a particularly high level of space utilisation. It can also be combined with a STILL EXV iGo high lift pallet truck or an autonomous mobile robot (AMR) to handle goods from the transfer stations.
Customer reference:
Find out what our customer Tarkett thinks of this solution.
Storage and retrieval (wide aisle or block storage)
You have to handle palletised goods in wide aisle racking or block storage. These are most commonly used due to their high throughput speed.
Our solution:
The fully automated STILL FM-X iGo reach trucks or STILL EXV iGo high lift pallet truck are ideal for long distance transport or for storing and retrieving goods at high heights. They help you increase capacity or enable a 24/7 production.
Order picking
You may be fulfilling a customer order, handling multiple shipments of spare parts, or replenishing your production with new raw materials. Bulky, compressible and fragile items often still need to be picked manually. An autonomous order picker - in combination with pick-by-voice - can increase picking rates by following and positioning itself optimally for the operator.
Our solution:
The OPX iGo neo autonomous order picker follows operators wherever they go, effectively reducing their workload. Thanks to the intelligent analysis performed by its sensors, it also accurately and proactively detects its surroundings, obstacles and distances.
Customer reference:
See how the order picking efficiency was increased at Migros Verteilbetrieb AG
We use our expertise to help you analyse your processes and identify automation potential for your company. You decide whether you would like to take advantage of our additional consulting services. The services are carried out by experienced STILL intralogistics experts and include the following steps in detail:
Analysis and project qualification
We analyze your existing material flow processes, work with you to identify optimization potential and check whether the necessary framework conditions are in place for a successful automation project.
Conception and feasibility check
Based on the analysis, we develop a tailor-made automation concept for your intralogistics - including a comprehensive feasibility check.
Transparent offer
In the next step, we will provide you with a detailed offer that covers all aspects of your automation project.
Project planning
In close coordination with you, we plan all project steps carefully in advance and thus ensure a smooth implementation of your automation project.
Implementation
Our experienced automation experts take care of the implementation and integration of the solutions into your existing systems and structures.
Service and support
We support you in partnership – even beyond implementation. With our continuous service and maintenance offerings, we ensure the long-term success and efficiency of your automation solution.

Our services for your automated systems
Please fill out the form below. We will get back to you as soon as possible.
Fill out the form
Please fill out the form below. We will get back to you as soon as possible.
Call your expert advisor
The direct wire to your expert advisor
Request to: Automation in logistics
Please fill out the form below. We will get back to you as soon as possible.
You might also be interested in
Automation solutions from STILL
Not every automation solution makes economic sense for your individual requirements. We accompany you as partners in the selection of the appropriate automation level.
Automation with assistance systems Level 1 - Assisted driving
At this level, the driver is supported in his tasks by various intelligent assistance functions on his truck, but remains responsible for navigation in every situation. For example, with individually programmable warnings and situation-related speed adjustments, STILL enables highly safe and fatigue-free work with manual control.
Automated Industrial Trucks Level 2 - Partially Automated Driving
This level of automation includes solutions that enable vehicles to navigate in the warehouse partially on their own using special software or artificial intelligence and sensors. This makes them an intelligent partner for their users. Equipped accordingly, order-picking vehicles can follow their operators wherever they go and narrow-aisle trucks can be moved semi-automatically to the correct pallet position along the optimal path. The driver, however, remains responsible for the actions of his forklift at every step. Semi-automated vehicles in this way relieve the employee and increase both the productivity and the safety of your warehouse.
Automated Guided Vehicles Level 3 - Fully Automated Driving
Self-driving industrial trucks for automating internal logistics are now being used successfully by many industry leaders - and have been proven to significantly increase handling performance. With standardised automation kits, individual STILL series trucks can be automated for different process requirements within a very short time and scaled up to form a fully automated logistics process.
To implement a fully automated supply chain, we complement the iGo systems portfolio with solutions from our group sister DEMATIC, the world's leading supplier of integrated automation technology. This allows you to benefit from the advantages of a perfect interplay between automated STILL series trucks and stationary DEMATIC automation solutions, such as conveyor, distribution and sortation systems, stacker cranes or AutoStore systems.