The digital data duplicate
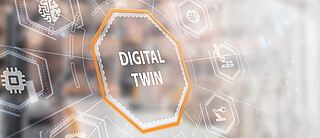
With the so-called digital twin, real situations are permanently transferred to a digital copy in real time. This opens up a wide range of possibilities, particularly in intralogistics and warehousing. We explain why this technology is so inviting to creative ideas for the future.
The 'digital twin' is one of those terms that immediately capture our imagination. It is often visualised with holographic models: service technicians working in the midst of a three-dimensional, lifelike digital image. “Reality looks different," says Dennis Schüthe, project manager at STILL. But that does not make it any less fascinating. It just takes a little more creative imagination to see concrete applications.
What is a digital twin?
In essence, the digital twin can be defined as follows: An object or situation from the real world is given a digital image - with the digital and real worlds constantly exchanging data with each other. A classic example would be a machine, where all relevant information is constantly fed to a computer, so that it can provide accurate information about what the machine is doing and what is happening around it.
A virtual image of the warehouse
The advantage results from this comprehensive knowledge: engineers can permanently monitor the machine, managers can continuously calculate expected turnover, service technicians can remotely estimate maintenance requirements. But the possibilities do not end there - and it is not just machines that can be mapped. It is also possible to create a digital image of entire facilities and systems, such as an entire supermarket or a city's water supply system - or even a warehouse.
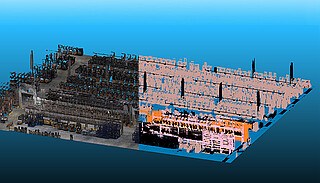
The digital twin also opens up numerous opportunities in intralogistics. STILL participated in the major research project ARIBIC (Artificial Intelligence-Based Indoor Cartography), in which renowned partners from industry and research tested how 3D maps of warehouses can be visualised in real time. "This is the basis for the intralogistics of the future," says Schüthe. What is special about this is that the digital map not only records data points, but also interprets them: "Is it a person, a pallet or a fire extinguisher?" explains Schlüthe. With this database and the appropriate software, it would be possible to do what warehouse management systems (WMS) have been promising to do for years, but are often failing to do adequately in practice: The flow of goods, traffic or capacity utilisation could be tracked precisely in real time. In reality, existing programmes often fail because of the 'human factor', as Schüthe explains: "If the WMS tells you that a pallet is to be stored in a certain place, but the employees on site agree that the shelf below is much more practical and mostly empty, no software can help at the moment."
Sensors collect data
A complete digital twin of the warehouse could open up new possibilities for intralogistics companies in the future: products could be tracked in real time, and entire warehouse architectures could be redesigned and perfected based on the data sets. Service providers such as STILL could develop and plan their optimisation proposals remotely and precisely, without the need for time-consuming on-site observations. This is still a dream of the future and will depend in particular on how well the corresponding software applications can be developed - and how comprehensive the database is.
This is because the success of a digital twin model stands and falls with the database in all application examples. "Put simply, a digital twin is basically a database," says Schüthe. Not only does this data need to be analysed and interpreted by artificial intelligence, it also needs to be collected in a meaningful and comprehensive way. Sensors are therefore crucial: depending on the application, they may have to measure not only visual information, but also temperature, pressure, acceleration or gravity. Creating a database for this is anything but trivial, and this is where ARIBIC's research is focused.
Digital twin fundamentally improves service
STILL is already taking advantage of the many benefits of this technology, for example in the service of automated vehicles. The digital twin supports service technicians in their daily work: components can be configured for a vehicle and then stored in the cloud. This ensures that the technician always has the right software on the right vehicle," says Hubert Klosterberg, service expert at STILL. The standardisation of software and hardware plays a key role in this: "We no longer have to train technicians specifically for a project. In future, every trained technician will be able to carry out standardised tasks for every customer.
In addition, with the digital twin, STILL service technicians can configure new hardware quickly and easily with a backup from the cloud and install it directly on site: "This significantly increases the availability of the trucks," says Klosterberg. It is also possible to continuously optimise the products.
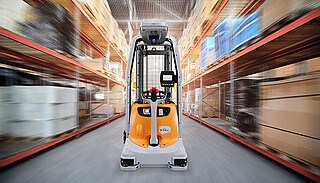
At first glance, the 'LernFFZ' project is a completely different application. The idea is for autonomous vehicles to learn how to behave from real human drivers. "It is a bit like a parent demonstrating something to a child so that the child can imitate it," says Lukas Hindemith, project manager at STILL. To do this, the truck must first be exposed to as many situations as possible, especially manoeuvres, movements and borderline cases that rarely occur. For this purpose, STILL is currently building a simulator as a digital twin, which will then be controlled by human drivers. Furthermore, the automated vehicles will then ideally have to learn new driving strategies on their own. "This only works well if there are as many failures as possible," says Hindemith: "You learn from mistakes - this also applies to the vehicle. The vehicle therefore trains as a virtual image. After all, nobody wants to cause damage to real warehouses and forklift trucks.”
Training in the virtual mirror world
This consideration is similar to another application: the welding simulator used in the training of construction mechanics at STILL. The welding helmet that the trainees put on has a screen. The real environment merges with the simulation. The augmented reality simulation turns plastic sheets into solid sheet steel and a plastic block into a welding nozzle. The advantage: not only can training take place without heat and smoke, i.e. without the need for expensive protective equipment - the trainees also receive real-time feedback on how fast they are working, at what distance and angle, and how they should position themselves correctly. "The augmented reality welding simulator trains muscle memory to a certain depth," says Maximilian Schwenn, training manager at STILL. "This would otherwise only be equivalent to intensive one-to-one supervision." There is less risk of accidents, material consumption is significantly reduced and the trainees demonstrably learn much faster: "Of course, the first welding seam under real conditions in the welding booth does not look the same as it does on the simulator," explains Schwenn, "but the changed environment is quickly adapted to what has been learned and great results can be achieved."
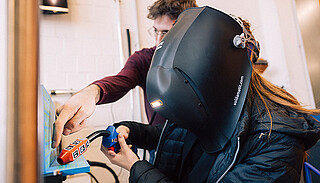
A real-time digital image of a warehouse, a virtual copy of a forklift truck or a perfect training simulator - none of these imaginative ideas is the 3D hologram described at the beginning. But the variety of possibilities already shows the different directions in which the technology could be used. A decisive factor for further applications will also be the creativity of service providers such as STILL - especially in conjunction with the ideas and requirements of customers for their individual solutions. So even if some user interfaces may look more like a spreadsheet at first glance, no one should be fooled: Few technologies currently hold as much future vision and creative potential for intralogistics as the digital twin.
Comments
No comments
Subscribe to our blog!
As soon as a new article is published, we will notify you! You can unsubscribe at anytime.
Leave a comment