The Future of Automation in Warehousing and Logistics; Trends for 2023 and Beyond
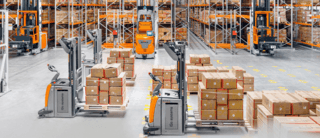
The warehousing and logistics industry is in the midst of a major transformation with the increasing adoption of automation. The need to maximise productivity and efficiency, while reducing operating costs and wastage is one of the biggest challenges facing warehouse managers – challenges which can be met with the implementation of automated or semi-automated processes. Yet it is estimated that around 80% of global warehouses have no automation at all.
Despite this, industry experts are already predicting an increase in automation over the next five years, driven by increasingly affordable technology, an ongoing labour shortage and the need to maximise efficiency and output.
The History of Warehouse Automation
Automation in warehouses has been a gradual process that has developed over many years. The use of basic automation technologies such as conveyor belts and forklifts, began in the early 20th century.
The more sophisticated automated systems we see today have only become widely used in the last few decades. One of the earliest examples of modern warehouse automation was the introduction of Automated Storage and Retrieval Systems (ASRS) in the 1960s, which used computers to control the movement of goods within a warehouse. In the 1980s and 1990s, the introduction of computerised inventory management systems, barcode scanning, and other technologies led to further automation of warehouses.
In recent years, we have seen the introduction of advanced robotics, artificial intelligence, and other cutting-edge technologies in warehouse automation. These systems can operate autonomously or semi-autonomously and perform arduous or repetitive tasks which were previously done manually, helping to boost efficiency, worker safety and productivity.
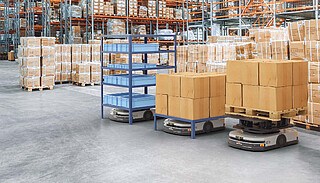
Type of Warehouse Automation Technology
Innovation in warehouse automation technology has resulted in significant changes in how the logistics industry operates and this progress shows little sign of slowing. These are some of the main warehouse technologies that are becoming increasingly commonplace.
Automated Guided Vehicles (AGVs)
Automated guided vehicles (AGVs), like the STILL iGo range, are mobile robots that are used to transport products within a warehouse. AGVs are programmed to follow a set path and can be equipped with sensors to avoid collisions with other objects. AGVs can be used to transport a variety of products, including pallets, carts, and individual items. Our Tugger Trains are a great example of this.
Robotic Picking Systems
Robotic picking systems use robotic arms used to pick and pack products within a warehouse. These systems can be used to handle a wide range of products, including items of different shapes and sizes. Robotic picking systems can improve accuracy and speed in the picking process, while also reducing the risk of injury to workers.
Autonomous Mobile Robots (AMRs)
An Autonomous Mobile Robot (AMR) is a type of robot that is designed to move and operate in a physical environment without the need for direct human control or intervention. These robots are equipped with sensors, processors, and control systems that enable them to navigate their surroundings, avoid obstacles, and perform tasks or missions without human supervision.
AMRs are capable of performing complex or repetitive tasks that would normally require human intervention, such as identifying and retrieving objects, following a predefined path, and adapting to changes in the environment. This makes them a valuable tool for businesses and industries that need to improve efficiency, productivity, and safety in their operations.
Automated Storage and Retrieval Systems (AS/RS)
Automated storage and retrieval systems (AS/RS) are robotic systems that handle the storage and retrieval of products within a warehouse. AS/RS systems use computer-controlled cranes to move products from one location to another, with minimal human intervention. These systems can handle a large volume of products and can also optimize space utilization within a warehouse.
Conveyor Systems
Conveyor systems are used to transport products within a warehouse, typically from one processing area to another. Conveyor systems can be automated using sensors and other technology, allowing for faster and more efficient product movement. Conveyor systems can also reduce the need for manual labour, as they can handle many of the tasks that would otherwise require human intervention.
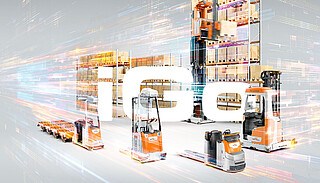
Warehouse automation trends for 2023
So, what does the future of warehouse automation look like in 2023?
Warehouse space will continue to be at a premium
With rising rents and economic uncertainty keeping warehouse space at a premium, companies are increasingly expected to do more with less. Limited floor space means every inch will continue to count and automated solutions will need to work within these restrictions. Whether it’s narrow aisles, high racking or tight turning circles, we expect to see automated solutions – like most technology – becoming smaller and more agile to fit the needs of the modern warehouse.
Machine learning in logistics will expand
Automated technology is one thing, but intelligent technology combines the efficiency and reliability of automation with the knowledge and understanding of your operations. AI-powered systems can optimise warehouse operations by predicting demand and managing your warehouse fleet and it’s likely we’ll see further synergy between automated hardware and intelligence software.
Labour shortages will drive demand for automation
With labour shortages set to continue to impact warehouses in 2023, we can expect to see an increase in businesses looking to automation to solve their staffing shortfall with fully or semi-automated processes.
Data shows its worth
We’ve already highlighted machine learning as a growth area for 2023, but a machine can only learn from the information it’s given. With that in mind, things like expected warehouse output, fleet performance, seasonal spikes in demand and inventory levels become the foundation on which any machine learning is built. If you don’t have this information already and you want to move to intelligent automation, you may find yourself on the backfoot as your system has nothing to learn from. If you would like to enquire about any of our services or Automated Guided Vehicles, speak to one of our experts, today.
Comments
No comments
Subscribe to our blog!
As soon as a new article is published, we will notify you! You can unsubscribe at anytime.
Leave a comment