How to Choose the Best Warehouse Racking System
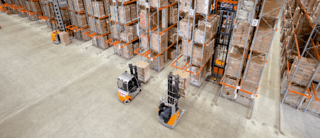
When managing a warehouse, it’s important to carefully consider the racking systems that you install. This decision can significantly impact logistic operations within any business, giving increased operation efficiency, a safer working environment and more economical storage if you choose the most suitable option. Choosing incorrect racking for your warehouse however can create an inefficient storage and operations system at best and a potentially hazardous working environment at worst.
In today’s “on-demand” environment, effective inventory management is vital when it comes to streamlining warehouse operations. Ultimately, your warehouse can only be as efficient as your storage solutions. When your goods are unorganised and difficult to retrieve or catalogue, it’s harder for operators to remain productive and motivated and more difficult for managers to plan effectively.
So, if you’re looking for the best racking and storage solutions for your warehouse, here are a few tips to help you make the right choice.
Choose the right type of racking system
This may be an obvious factor, but there are lots of different options and varieties of racking systems available on the market. Listed below are some of the racking systems on the market and their USPs which make them suited to specific requirements.
Pallet Racking
Pallet racking is a simple, versatile racking system that lets you store goods on pallets from floor to (almost) ceiling. These racking systems give maximum adaptability in warehouses spaces and give clear access to and visibility of stored goods.
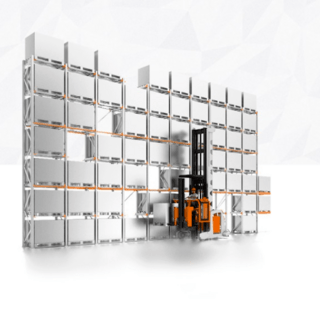
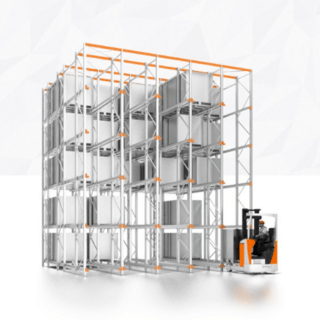
Drive-in and Drive-through Racking
This compact racking system lets you store a large number of identical products behind one another, storing “deep” rather than “high”. Trucks can move in out of the rack channels to remove and store goods. These systems often work on a LiFo principle (Last in, First out) but it is possible to operate a FiFo (First in, First out) system if that works better for certain warehouses.
Pallet Shuttle Systems
These high-density racking systems maximise storage volume in restricted spaces and allow for the semi-automatic storage and retrieval of goods. The truck drops the pallet of goods at the entry point to the rack channel where it’s picked up by the shuttle and moved to the end of the channel (or next available storage space). Unlike the Drive-in Drive out system, the truck doesn’t enter the channels and the pallet can later be retrieved by reversing the process.
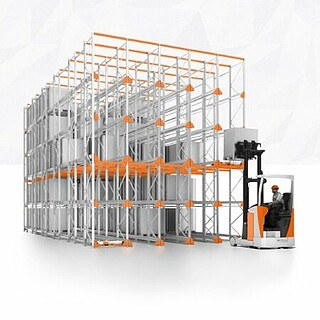
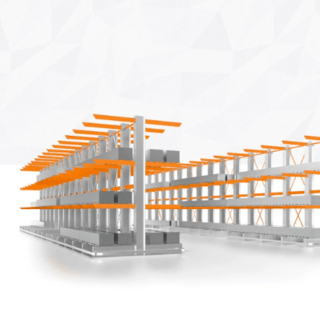
Cantilever Racking
If you’re looking to store bulky or long goods, cantilever racking is a good option. The design means there’s no need for front struts which allows for easy access to your inventory, as well as secure storage.
Push Back and Pallet Flow Racking
If your warehouse has a high turnover and goods often don’t stay in storage long before moving out again, push back and pallet flow racks are a good solution. The dynamic rack system automatically moves good to the front of the rack face, making them ideal for order picking or deep storage of identical goods.
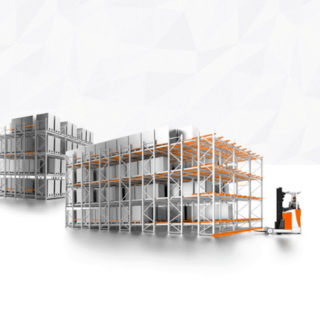
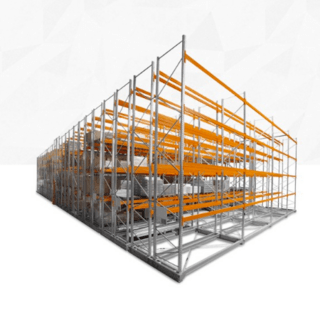
Mobile Racking
Mobile racking makes the maximum use of available warehouse space and allows you to use just one aisle for storage and retrieval. The aisles are mounted on carriages and moved by motors, meaning that each storage location can be access by moving the rack.
Look for flexible solutions to meet tomorrow’s needs
While it’s impossible and not entirely practical to plan too far ahead, it’s always worth futureproofing any investment as much as possible. While we don’t suggest you install a racking system that isn’t really suitable but may become efficient in five years’ time, it is definitely worth building in flexibility wherever possible, so you’re not rigidly confined by a system if you need a bit of leeway. A good example of this type of flexibility would be STILL’s Pallet Rack system which can be configured individually and adapted to fit your warehouse space, as well as to the weight and distribution of your stored goods.
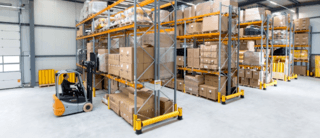
Think about your vertical space as well as horizontal
When your start to run out of horizontal floorspace in a warehouse – or any commercial property – you have two options. Acquire more floorspace, often at significant cost, or maximise your vertical space. This is where high racking systems and shelving can really provide value for money. By utilising your vertical space, you could increase your storage capacity many times over (depending on your existing set up) without increasing your warehouse footprint by a single inch.
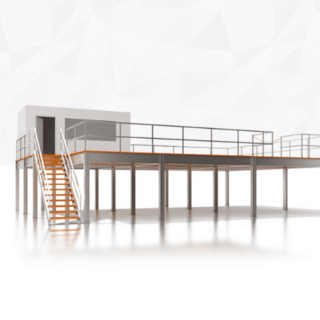
Consider your warehouse floor space
In your warehouse, aisle space is an important thing. Reducing the aisle width will mean there is less space to manoeuvre, which will mean that your drivers are more likely to collide with the uprights of racks and have more accidents. In addition, less aisle space can cause forklift drivers to load and retrieve inventory more slowly, compromising workflow. This is where an optimised vehicle fleet can work with specialised racking solutions and additional driver assistance features can reduce the risk of collisions and damage in confined spaces. VNA Trucks can be invaluable here as they are specifically designed to work efficiently in high, narrow aisles to make the most of the space available. It’s important to consider the whole warehouse operation when choosing a racking solution.
Factors like these are essential in maintaining your businesses high standards, so choosing the right racking system is an essential element of warehouse logistics. If you’d like to discuss your warehouse racking requirements or speak to our experts about the options available to you, you can contact the team at STILL today.
Comments
No comments
Subscribe to our blog!
As soon as a new article is published, we will notify you! You can unsubscribe at anytime.
Leave a comment